First responders and military personnel are routinely exposed to various types of hazards in their line of duty, ranging from extreme temperatures, fire, chemicals, ballistic threats, and more. As such, personal protective equipment (PPE) is crucial for ensuring their safety and ability to perform their duties effectively.
For this Expert Interview, we sat down with Colin Whittaker, Business Development Manager at James Heal, to discuss the fabrics and garments used in first responder and military PPE, the functional attributes necessary for their effectiveness, and the test requirements and standards. Colin has first-hand experience in the manufacturing of textiles produced specifically for protective clothing.
What’s covered:
- PPE garments: the fabrics and how they are constructed
- Functional attributes of PPE fabrics
- Test requirements and related standards for PPE garments
- Choosing the right testing equipment for PPE fabrics and garments
PPE garments: the fabrics and how they are constructed
“First responder and military PPE fabrics are typically constructed using a combination of natural and synthetic fibres.”, begins Colin. “These fibres are usually woven together using specialised techniques to produce fabrics with the desired characteristics, such as strength, durability, and flame resistance.”
Synthetic fibres include:
- Meta Aramids (e.g., Nomex®, Teijinconex®)
- Para Aramids (e.g. Kevlar®, Twaron®)
- Polybenzimidazole (PBI), Polytetrafluoroethylene (PTFE)
Natural fibres include:
- Cotton and wool
“What differentiates protective clothing to standard apparel is that garments are designed with specific functions in mind to protect first responders and military personnel.” says Colin. These functions vary in specificity, due to the nature of how the garments are constructed, as each garment may consist of multiple layers, with each layer serving a specific purpose.
The most common functions of a PPE garment are to offer thermal protection, chemical resistance, and ballistic protection, or a combination of each - plus many others. “A good example of the functional layering system construction is a firefighter's turnout gear. This may consist of an outer layer fabric that is flame-resistant, a moisture barrier to protect against water and bloodborne pathogens, and an inner liner layer to provide thermal protection and comfort.” adds Colin.
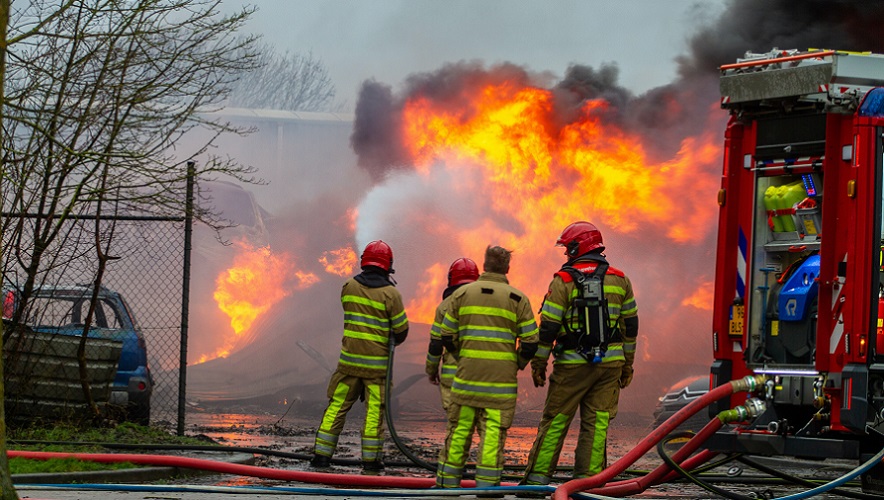
Colin Whittaker, Business Development Manager at James Heal“The construction of PPE fabrics and garments is complex, often involving specialised techniques and a combination of fibres to achieve the desired characteristics.”
Now, let’s dive into the specific functional attributes necessary for PPE fabrics and garments
- Flame resistance: This is a critical attribute for PPE fabrics and garments that will be exposed to heat and flame. Flame resistance can be achieved by using specialised technical fibres and fabrics, as well as the application of flame retardants.
- Thermal protection: First responders and military personnel may be exposed to extreme temperatures, which can be harmful to the body. PPE fabrics and garments must provide adequate thermal protection to prevent burns, heat exhaustion, and other injuries
- Chemical resistance: Chemical exposure can cause severe harm to the body, so PPE fabrics and garments must be resistant to chemical penetration.
- Ballistic protection: Military personnel may face ballistic threats, so PPE fabrics and garments must provide adequate ballistic protection.
- Water resistance: PPE fabrics and garments must be able to repel water to prevent moisture from penetrating the fabric and causing discomfort or reducing effectiveness. Moisture management and the rate of drying is extremely important.
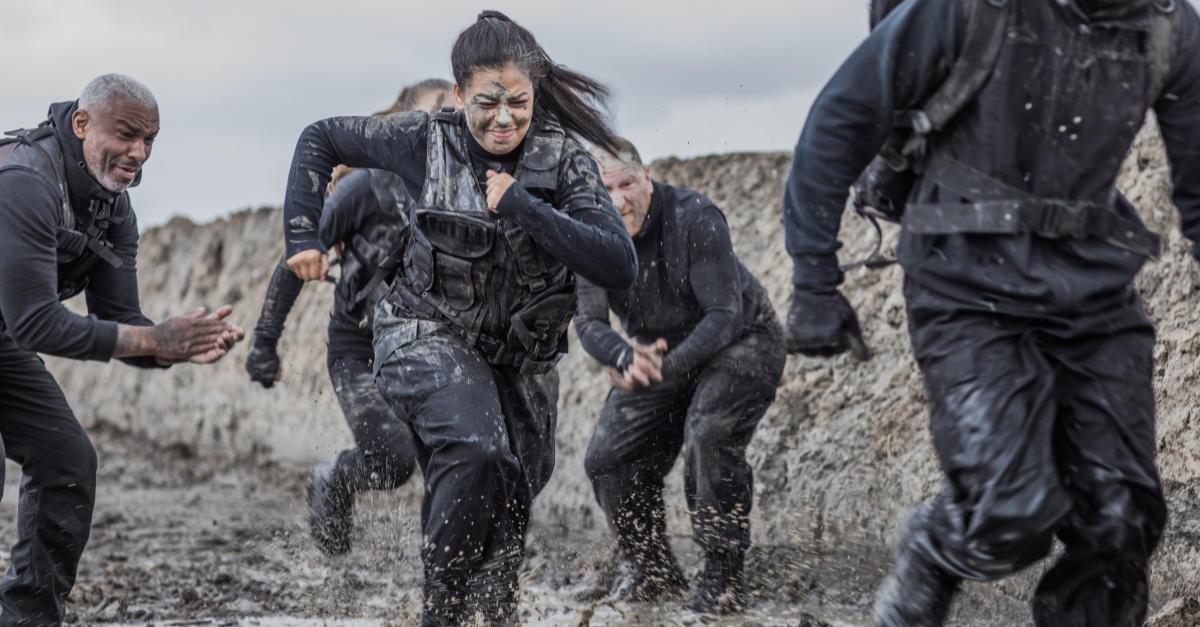
Test requirements and standards
“PPE fabrics and garments must be tested to ensure that they meet the necessary standards for effectiveness and safety.”
Some of the test requirements and standards for PPE fabrics and garments include:
- National Fire Protection Association (NFPA) standards:
These standards are mainly used in the Americas and cover various aspects of PPE for firefighters (Structural and Wildland), including thermal protection, flame resistance, and moisture barriers e.g. NFPA 1971 is a Standard on Protective Ensembles for Structural Fire Fighting and Proximity Fire Fighting covers the design, construction, performance, and certification requirements for structural firefighting gear, including helmets, gloves, boots, turnout coats, and turnout pants. The standard specifies minimum performance levels for various aspects of the gear, such as thermal protection, water resistance, and overall durability. In addition, the standard requires that all components of the ensemble be tested as a system to ensure they work together effectively to protect the wearer.
- ASTM International standards:
ASTM standards cover a wide range of PPE, including chemical protective clothing, ballistic-resistant body armour, and more e.g. ASTM F1506 is a standard that covers the performance requirements for flame-resistant (FR) clothing used in the workplace. It specifies the minimum performance requirements for FR fabrics and garments, including flammability, thermal shrinkage, and heat resistance.
- European Norm (EN ISO) standards:
These standards are mainly used in Europe and cover various aspects of PPE for firefighters, military personnel, and others e.g. EN 469: Protective clothing for firefighters is a standard that specifies the minimum performance requirements for protective clothing for firefighters. It includes requirements for thermal performance, water resistance, and resistance to mechanical risks such as abrasion and puncture. The standard also includes requirements for the design and construction of the clothing, such as visibility and ease of movement.
“Compared with mainstream fashion garments, performance fabrics have technical or functional benefits, for comfort and/or safety. The rise in these fabrics means there is a need for new and improved technology for testing their performance to back up their claims.”
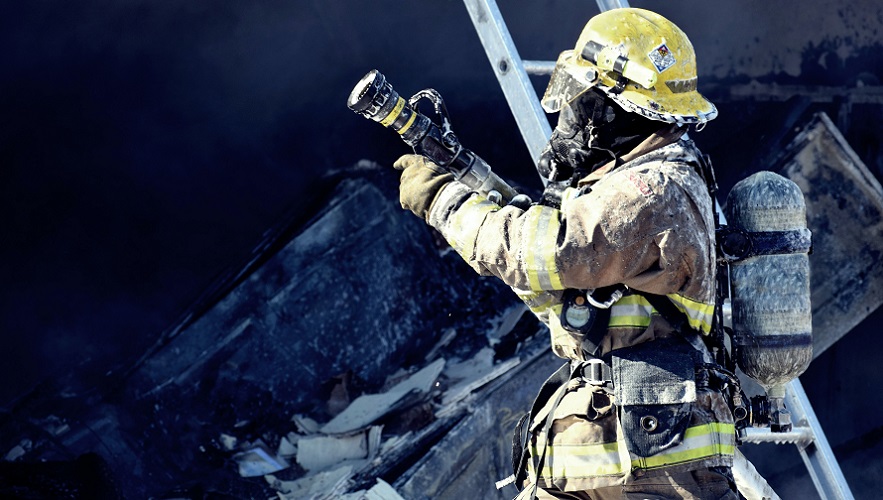
Choosing the right testing equipment for PPE fabrics and garments
“At James Heal, we understand that PPE fabrics and garments are critical for protecting first responders and military personnel in hazardous environments.” says Colin.
“Crucially, for optimum performance and safety for the wearer, these fabrics must be routinely tested at each stage of the production cycle to ensure that they meet the necessary standards for effectiveness and safety. Precision testing instrumentation that guarantees accurate, repeatable and reliable results is essential.”
James Heal Performance Testing Instruments for PPE:
AirPro - Air permeability testing
AquAbrasion - testing wear and abrasion under wet conditions
HydroView - hydrostatic head pressure testing
ProDry - drying rate testing
TruRain - water repellency for Bundesmann artificial rain shower testing
WickView - moisture management testing or wicking testing
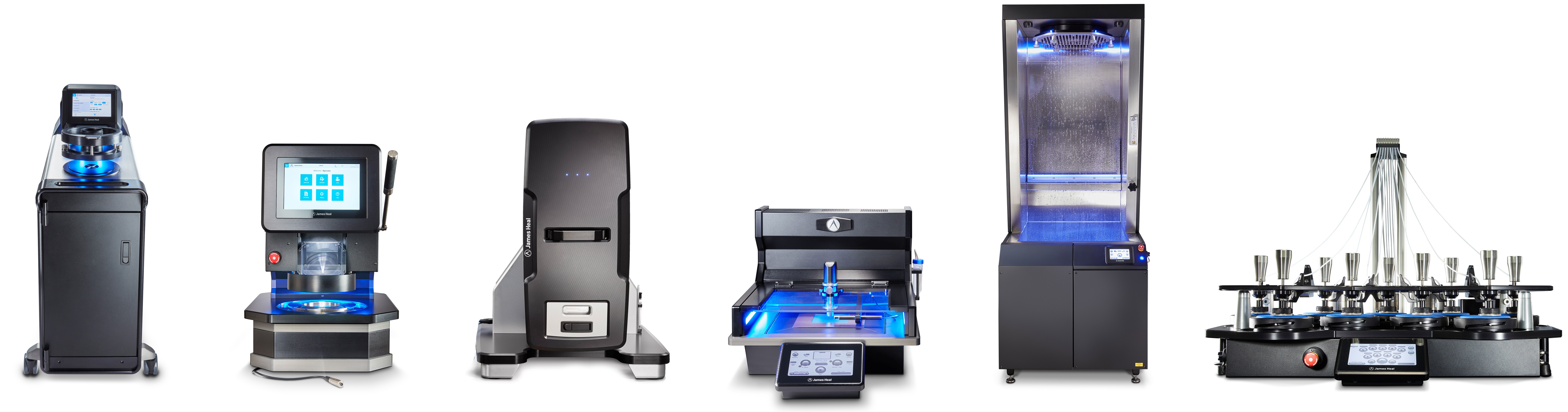
Traditional test instruments for PPE:
FlexiBurn - flammability testing
Martindale - traditional wear and abrasion testing
Titan - tensile strength testing, durability testing for attachments, and compression testing
TruBurst - bursting strength testing
TruFade - colour fastness to light testing
ElmaTear - testing for tear strength
FlexiFrame - stretch and recovery testing
ProMace - test for snagging
Impulse - random tumble pilling testing
AccuDry, DynaWash, GyroWash and Wascator - laundering testing
And more! Take a look at the full range James Heal of textile testing instruments.
To learn more about our performance testing instruments for PPE garments and fabrics, visit our performance testing microsite.

Enjoyed this article?
Check out our series of articles and case studies on protective wear testing and more in our News & Insights section.
If you have any questions or would like to discuss your requirements for protective wear and PPE testing, please get in touch.