In this case study we discover how with the support of James Heal, Engelbert Strauss brought their in-house laboratory vision to reality, in a large-scale project which incredibly was led by a Lab Manager completely new to textiles testing.
Where it all began
Three years ago, Lab Manager Lucien Nehl (pictured) was working on a logistics project within Engelbert Strauss. His next challenge? To project manage the inception of a brand-new in-house test laboratory. We talked to Lucien about the reasons for establishing the lab, his role and how he successfully achieved the end result.
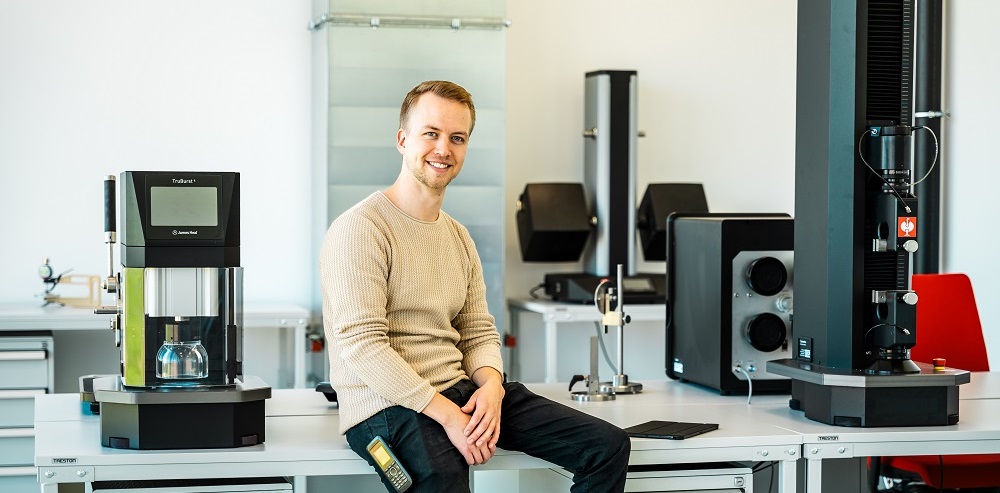
Headquartered in Biebergemünd, Germany, Engelbert Strauss GmbH & Co. KG, is a worldwide leading mail order and retail company for workwear, work shoes, and general work and industrial supplies. The company also has a successful children's clothing range. Founded in 1948, the German family-owned company employs nearly 1,700 people, and offers its own textile finishing with embroidery, printing and laser technology, among other processes.
The company operates its own shoe production facility in the state-of-the-art STRAUSS CI Factory in Schlüchtern, in addition to its headquarters in Biebergemünd. Built in 2020, the CI Factory has a development department for the latest types of textile finishing. Moreover, it houses the testing laboratory established by Lucien Nehl to focus on textiles and footwear testing.

A further production site located in Chattogram, Bangladesh is a workwear academy as well as a development centre for Engelbert Strauss, providing connected small series production. In collaboration with the STRAUSS CI Factory in Germany, the CI Factory in Chattogram forms a tandem production unit that working together provide rapid solutions to the demand for continuous innovation in textiles composition and performance, keeping Engelbert Strauss products at the forefront of their sector.
Solving the biggest challenges
With new catalogue collections being launched in both Spring and Autumn each year, Engelbert Strauss wanted faster results and greater control over their testing processes. They needed to be more responsive with the ability to quickly inform product development, shortening the cycle from design through to commercial production. The team recognised that having an in-house lab was the best way to achieve their objectives.

The development of a new in-house lab was in itself a huge challenge, but not one that was taken lightly by Lucien. The aim was to not only set up their own in-house lab to facilitate faster, more responsive feedback for R&D and quality control, but also to establish a professional laboratory equipped to offer extremely high standards of testing. This meant establishing new processes within the company, gaining an understanding of the different priorities in each department, and much collaboration to deliver the company’s objectives.
Setting up the new lab
The first steps towards establishing an in-house lab at the brand-new STRAUSS CI factory had already been made in 2020, with the phase 1 installation of a James Heal Titan 5 universal testing machine, and an AquAbrasion wet abrasion tester.
Detailed research, evaluation and planning went into phase 2, which was completed mid-2023 with the installation of whole series of James Heal instruments procured by Lab Manager Lucien Nehl.
Lucien manages the complete textiles testing facility, and started working with an excellent, highly motivated team on product testing. In total around 70 different tests are undertaken on garments, footwear and accessories. These include abrasion and pilling, colour fastness, laundering, snagging, light fastness, compression, burst strength and durability tests.

Footwear testing is done to standard ISO 20344 for safety shoes. The lab team tests toe caps, compression, continuous flex, sole puncture resistance, electrical resistance and slip resistance.



Digital focus
The processes of the new STRAUSS test laboratory were planned and mapped completely digitally. The lab operates as a paperless environment and all employees have their own tablet with which they can scan samples via QR codes, document test results and even create fully automated reports. The departments of STRAUSS can monitor the flow of their samples through the laboratory in real time via a dedicated online 'customer zone'.

Industry trends
Thinking about industry trends, as might be anticipated Lab Manager Lucien identifies sustainability as probably the main factor leading change in the textiles industry. Engelbert Strauss is already ahead of the curve in product development when it comes to utilising new sustainable fibres in its products.
"Sustainability is one of the focal points at the CI Factory”, says Lucien. STRAUSS achieved a world first in November 2022, having developed the first fully biodegradable work trousers made from banana fibres, organic cotton and bamboo. The natural dyes used in the e.s.botanica sustainable workwear line are derived from agricultural by-products, such as beetroot, nutshells and leaves.
The development team at the STRAUSS production facility designed the e.s.botanica collection. The first prototypes were constructed at the CI Factory, Schlüchtern, and in close collaboration, a small series batch run was produced in the development centre of the CI Factory in Chattogram, Bangladesh (pictured below).
Having an in-house lab with the ability to test and quickly feedback results to inform R&D, future product development time will be reduced, speeding up the whole innovation process.

Working in partnership - why James Heal?
Having two James Heal instruments already installed in 2020 prior to taking up his post, Lucien Nehl began working with the James Heal team in Germany and built up a great working relationship. When the time came to establish an all-encompassing new lab, there was an obvious choice, "Having a long-term partnership and the ongoing support and guidance that I get from the James Heal team is invaluable, along with the textiles testing expertise provided. I knew this relationship would be critical to the success of implementing the project." says Lucien.
Head of Sales for James Heal in Germany, Lutz Gerold, provided help and advice on setting up the new lab. "I experienced that Lutz always responded as quickly as possible to our requests and problems and was personally committed to the success of our project. Previously he helped us with the adaptation of our Titan 5 instrument enabling it to undertake a sole puncture test by adding a custom accessory to verify the test requirements for puncture-resistant footwear." continues Lucien.

Customer support was a major factor in choosing James Heal as a partner, but also reliability and the impression that the instruments give. Lucien says, "A lot of effort was being made to create a professional lab with high standards. Since the lab can be visited by business partners, appearance also played a major role, although obviously not as big a role as the reliability of the testing machines."
"James Heal instruments certainly give the impression of being very robust in quality, and their innovative brand, clean lines and consistent black design create an immediate impact, all adding to the perception of a lab that provides very high standards and professionalism." Lucien adds.
"Knowing that James Heal instruments were already being used in accredited labs also gave me confidence that these were the right choice for what we wanted to achieve." concludes Lucien.
What about the STRAUSS Lab team?
The Engelbert Strauss lab technicians give a prompt answer when asked about their favourite features of James Heal instruments; their touchscreen, intuitive software and the fact they’re easy-to-use and of premium quality.
Reliability was another factor with installation and set up running smoothly, and having the James Heal team on hand to assist, knowing someone is available to answer technical questions and quickly provide solutions, was cited as a real benefit. The convenience of local support for service and calibration and the availability of test materials provides the full package.

And finally
Rounding up our discussion, we talked about future innovations and ongoing collaboration, with Lucien anticipating continued development and growth in sustainable fashion and the potential for new technology moving forward.

A last word from James Heal’s Lutz Gerold on the partnership with Engelbert Strauss, "It is not an everyday situation where a new lab is to be set up by someone new to textile testing. However, there were no critical challenges from our perspective, as everything was so well prepared for the installation, making it very straight forward. An incredible achievement by Lucien and Engelbert Strauss - it was a pleasure to work on this project!"
Lutz will be speaking at the Aachen-Dresden-Denkendorf International Textiles Conference on 1 December, where his presentation 'Workwear and performance wear - Testing function, protection and comfort', will focus on an Engelbert Strauss product by way of example.
James Heal products used in the Engelbert Strauss lab include:
- Titan 5 - Universal strength tester
- AquAbrasion - Wet (and dry) abrasion and pilling tester
- TruBurst - Burst strength tester
- TruFade - Lightfastness tester
- ElmaTear - Tear tester
- Orbitor - Pilling and snagging tester
- Impulse - Random tumble pilling tester
- GyroWash - Colour fastness tester
- CrockMaster - Colour fastness to rubbing
- Wascator - Standardised European washing machine
- AccuDry - Standardised European tumble dryer
- Crease recovery tester
- Perspirometers
- Sample Cutter - 100 cm²
- Test materials - laundry detergents, and consumables



